Flooding can be a homeowner’s worst nightmare, and a reliable defense is crucial. The oil sump pump serves as a primary line of defense against rising water levels in your basement or crawl space. Understanding the role of a check valve is paramount for optimal pump function, preventing backflow and ensuring efficient water removal. Many homeowners rely on brands like Zoeller for their proven track record of durability and performance in oil sump pump systems. Consulting a local plumbing expert can help you determine the best size and type of oil sump pump for your specific needs and prevent potential water damage.
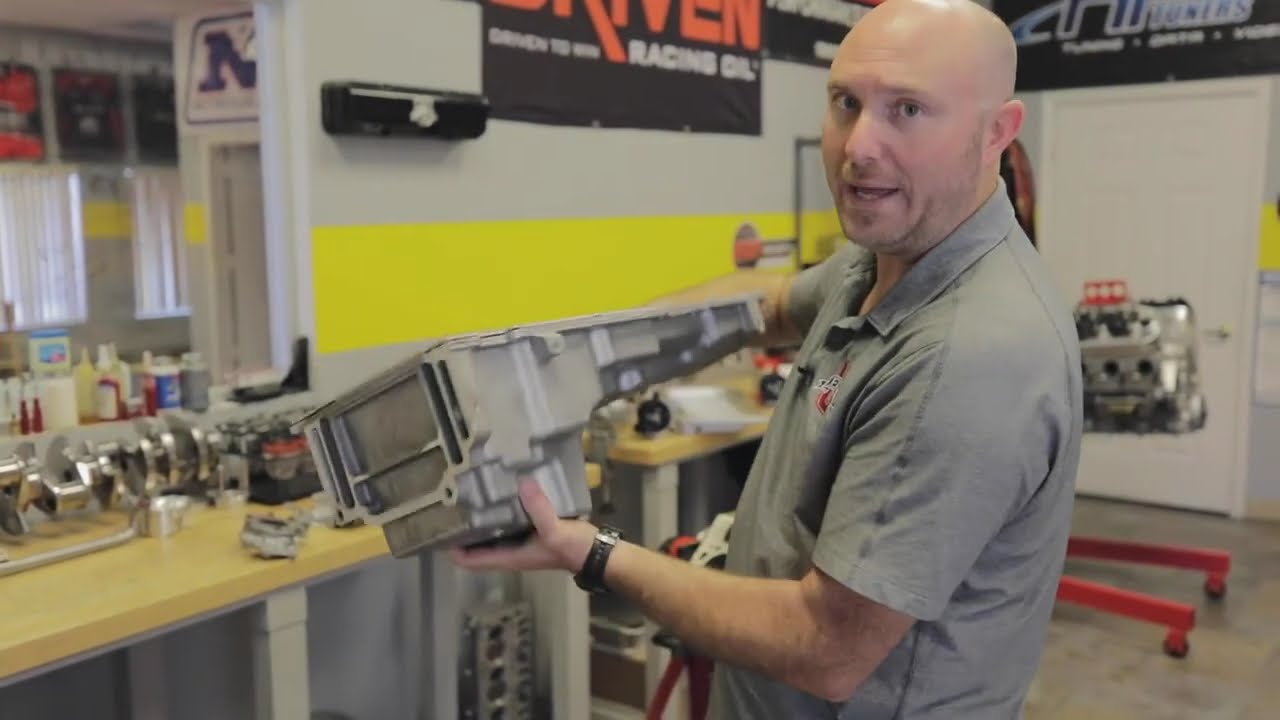
Image taken from the YouTube channel EFI University , from the video titled Everything you need to know about a dry sump oiling system. .
Imagine waking up to a nightmare: ankle-deep water sloshing through your basement, the musty smell of damp carpet filling the air, and the chilling realization that your treasured belongings are being soaked and ruined. This isn’t a scene from a horror movie; it’s a reality for countless homeowners who underestimate the devastating potential of flooding.
The unfortunate story of the Millers highlights this reality. After a particularly heavy downpour, they awoke to find their basement transformed into an indoor swimming pool. Family heirlooms were destroyed, furniture was waterlogged, and the lingering dampness threatened mold growth. The cost, both financial and emotional, was staggering.
The Oil Sump Pump: Your First Line of Defense
But what if there was a way to significantly reduce the risk of such a disaster? Enter the oil sump pump, a small but mighty device designed to be your home’s silent guardian against the ever-present threat of flooding. An oil sump pump is more than just a piece of equipment; it’s an investment in peace of mind, a proactive measure to protect your home and valuables from water damage.
This comprehensive guide is designed to empower you with the knowledge and tools you need to effectively utilize an oil sump pump and safeguard your home. We’ll walk you through every aspect, ensuring you’re well-prepared.
What This Guide Will Cover
This guide takes you through the essential knowledge of flood prevention and water management.
-
Understanding the Threat: We’ll explore the common causes of basement flooding and the far-reaching consequences of water damage, revealing why proactive measures are essential.
-
Choosing the Right Pump: Selecting the correct oil sump pump is critical. We’ll analyze the key factors to consider, ensuring you make an informed decision that matches your specific needs.
-
Installation: A properly installed sump pump is a reliable sump pump. We’ll guide you through the installation process, emphasizing safety and best practices.
-
Maintenance: Regular maintenance is key to ensuring your sump pump operates effectively for years to come. We’ll provide practical tips and schedules.
-
Backup Power: Power outages can cripple your sump pump. We’ll discuss backup power solutions to ensure continuous protection.
-
Troubleshooting: When issues arise, quick diagnosis and repair can prevent major problems. We’ll equip you with troubleshooting skills.
Understanding the Threat: Why Basements Flood and the Devastating Consequences
Before we dive into the solutions, it’s critical to understand the problem. Basement flooding isn’t just an inconvenience; it’s a serious threat to your home’s structural integrity and your family’s health. Let’s explore the common culprits behind basement flooding and the potentially devastating consequences you might face.
Common Causes of Basement Flooding
Several factors can contribute to water intrusion in your basement. Identifying these risks is the first step in effectively protecting your home.
-
Groundwater: Groundwater is a persistent threat. The water table naturally fluctuates. During periods of heavy rain or snowmelt, it can rise above your basement floor level. This hydrostatic pressure forces water through cracks in your foundation, leading to seepage and, eventually, flooding.
-
Heavy Rainfall: Intense storms overwhelm drainage systems. Runoff saturates the soil around your foundation, increasing the risk of water intrusion. Poor landscaping that slopes towards your house exacerbates this problem, channeling water directly to your foundation.
-
Sewer Backups: Sanitary sewer systems can become overloaded during heavy rains. This can cause wastewater to flow backward into your home through floor drains and plumbing fixtures in the basement. Sewer backups are particularly problematic due to the unsanitary nature of the water, requiring professional cleanup.
The Devastating Consequences of Water Damage
Ignoring basement flooding can lead to a cascade of problems that affect your home’s value and your family’s well-being.
-
Structural Damage: Water weakens building materials. Prolonged exposure can cause foundations to crack, walls to bow, and wooden supports to rot. These structural issues are expensive to repair and can compromise the safety of your home.
-
Mold Growth: Damp environments are breeding grounds for mold. Mold spores can cause respiratory problems, allergies, and other health issues. Mold remediation is a costly and disruptive process, requiring professional intervention. Some molds produce toxins, making cleanup more dangerous.
-
Decreased Property Value: A history of basement flooding significantly reduces your home’s market value. Potential buyers are wary of water damage and the associated risks. Disclosure laws require you to inform potential buyers of any previous flooding issues, which can deter offers or lead to lower sale prices.
The Sump Pump’s Crucial Role
Understanding the risks highlights the necessity of a proactive defense. An oil sump pump is more than just a piece of equipment; it’s an essential component of a comprehensive water management strategy. By automatically removing water from your sump pit, it prevents water from reaching your basement floor and causing damage. In essence, it acts as a sentinel, standing guard against the ever-present threat of flooding.
Prolonged water exposure threatens your property, but understanding the underlying causes helps in prevention. Groundwater seepage, heavy rainfall, and even sewer backups can lead to significant water accumulation in your basement. Knowing what you’re up against is half the battle, which leads us to explore a critical tool in the fight against basement flooding: the oil sump pump.
Oil Sump Pumps Explained: How They Work to Keep Your Basement Dry
An oil sump pump serves as the frontline defense against basement flooding. It’s designed to automatically remove water that accumulates in a sump pit, a purpose-built basin typically located in the lowest part of your basement.
The Core Function: Automatic Water Removal
At its heart, the oil sump pump’s primary function is quite simple: to automatically detect rising water levels in the sump pit and expel that water away from your foundation, preventing it from reaching the basement floor. This automatic operation is crucial because it ensures that water is removed even when you’re not around to monitor the situation.
Key Components of an Oil Sump Pump System
An oil sump pump system isn’t just a single device; it’s an assembly of interconnected components working in concert. Understanding each component’s role will help you understand how it all works together to keep your basement dry.
The Pump Itself: Submersible vs. Pedestal
The heart of the system is, of course, the pump. Oil sump pumps come in two primary types:
-
Submersible pumps are designed to be submerged in the sump pit. They are generally quieter and more efficient at pumping large volumes of water.
-
Pedestal pumps have a motor that sits above the sump pit, with a hose extending down into the water. They are typically less expensive than submersible pumps, but they can be noisier and less efficient.
The Float Switch: Detecting Rising Water
The float switch is a crucial component that acts as a sensor. It’s a buoyant device that rises with the water level in the sump pit. When the water reaches a certain height, the float switch activates the pump.
The Sump Pit: Water Collection Point
The sump pit is a basin, typically made of concrete or plastic, installed below the basement floor. It serves as the collection point for groundwater and other water that seeps into your basement.
The Discharge Pipe: Expelling the Water
The discharge pipe is responsible for carrying the water away from the sump pit and your foundation. It typically runs outside your home and empties the water into a designated drainage area, such as a yard or storm sewer.
The Check Valve: Preventing Backflow
The check valve is a one-way valve installed in the discharge pipe. Its primary function is to prevent water from flowing back into the sump pit after the pump shuts off. This prevents the pump from having to re-pump the same water repeatedly.
Activation and Prevention of Backflow
The float switch is the key to automatic operation. As water accumulates in the sump pit, the float rises. Once the water level reaches a predetermined point, the float switch triggers the pump to turn on. The pump then begins expelling water through the discharge pipe.
Once the pump is on, the check valve swings open, allowing water to flow out of the basement. When the pump stops, the check valve prevents the water remaining in the discharge pipe from flowing back into the sump pit, ensuring efficient operation and preventing unnecessary wear and tear on the pump.
Prolonged water exposure threatens your property, but understanding the underlying causes helps in prevention. Groundwater seepage, heavy rainfall, and even sewer backups can lead to significant water accumulation in your basement. Knowing what you’re up against is half the battle, which leads us to explore a critical tool in the fight against basement flooding: the oil sump pump.
Choosing the Right Oil Sump Pump for Your Needs: A Buyer’s Guide
Selecting the right oil sump pump is crucial for effective basement flood protection. Not all pumps are created equal, and the best choice depends on your specific needs and basement characteristics. This section provides practical advice to guide your purchasing decision. We’ll examine the different types of pumps, key factors to consider, and why proper sizing is essential.
Submersible vs. Pedestal Pumps: Weighing the Options
The first step in choosing the right oil sump pump is understanding the two primary types: submersible and pedestal. Each has its own set of advantages and disadvantages.
Submersible Sump Pumps
Submersible pumps are designed to be fully immersed in the sump pit.
Here’s a breakdown of their pros and cons:
Pros:
- Quieter operation: Being underwater dampens the noise, making them significantly quieter than pedestal pumps.
- Longer lifespan: The surrounding water helps dissipate heat, extending the pump’s lifespan.
- Space-saving: They take up less space in the basement since they sit inside the pit.
Cons:
- More expensive: Submersible pumps generally cost more upfront than pedestal pumps.
- Difficult to service: Repairing a submersible pump requires removing it from the pit, which can be messy.
- Potential for clogging: Because they sit at the bottom of the pit, they can be more prone to clogs from sediment.
Pedestal Sump Pumps
Pedestal pumps are mounted above the sump pit with a pipe extending down into the water.
Here’s a summary of their pros and cons:
Pros:
- More affordable: Pedestal pumps are typically less expensive than submersible models.
- Easier to service: The motor is easily accessible for maintenance and repairs.
- Less prone to clogging: The intake is positioned higher in the pit, reducing the risk of debris clogging the pump.
Cons:
- Noisier operation: The motor is exposed, making them louder than submersible pumps.
- Shorter lifespan: The motor is more susceptible to overheating due to a lack of water cooling.
- Take up more space: They occupy more space in the basement due to their above-ground motor.
Key Factors to Consider When Selecting an Oil Sump Pump
Beyond the type of pump, several crucial factors influence its effectiveness in protecting your basement.
Horsepower (HP)
Horsepower indicates the pump’s power. Higher horsepower pumps can move more water and handle greater pumping heights. Choose horsepower based on your basement’s risk of flooding.
Flow Rate (Gallons Per Hour – GPH)
Flow rate measures how much water the pump can move per hour. This is a critical spec. Select a GPH rating that aligns with the expected volume of water your basement may encounter during heavy rainfall.
Pumping Height (Head)
Pumping height, or "head," refers to the vertical distance the pump needs to push the water to discharge it away from your foundation. Consider the distance from the sump pit to the discharge point when selecting your pump.
The Importance of Proper Sizing
Choosing the right size pump is crucial for effective flood protection. An undersized pump won’t be able to keep up with heavy water flow, while an oversized pump can cycle too frequently, shortening its lifespan and wasting energy.
Consider your basement’s square footage, the typical rainfall in your area, and the depth of your water table when determining the appropriate size pump. Consult with a plumbing professional if you’re unsure about the proper sizing for your specific situation.
Prolonged water exposure threatens your property, but understanding the underlying causes helps in prevention. Groundwater seepage, heavy rainfall, and even sewer backups can lead to significant water accumulation in your basement. Knowing what you’re up against is half the battle, which leads us to explore a critical tool in the fight against basement flooding: the oil sump pump.
Installation: Setting Up Your Sump Pump for Optimal Flood Protection
Once you’ve chosen the right oil sump pump for your needs, proper installation is paramount. A correctly installed pump provides the most effective defense against basement flooding. This section provides a comprehensive, step-by-step guide to setting up your sump pump, emphasizing safety and optimal performance.
Step-by-Step Installation Guide
Follow these steps carefully for a successful sump pump installation:
-
Safety First: Disconnect Power. Before you begin any work, always disconnect the power to the outlet you will be using for the sump pump. This is crucial to prevent electrical shock. Use a circuit tester to confirm the power is off.
-
Prepare the Sump Pit. Ensure your sump pit is clean and free of debris. A clogged pit can hinder the pump’s operation. The pit should be deep enough to fully submerge the pump (if submersible) or accommodate the float switch mechanism.
-
Positioning the Pump. Place the pump securely in the sump pit. For submersible pumps, ensure it’s resting on a stable surface, away from the bottom of the pit to prevent sediment from entering the pump. Pedestal pumps should be positioned so that the motor is clear of any potential water level.
-
Connecting the Discharge Pipe. Attach the discharge pipe to the pump’s outlet. Use the appropriate fittings and clamps to ensure a watertight seal. The discharge pipe should run upwards and away from your home, typically exiting through a basement wall or window.
-
Installing the Check Valve. The check valve is essential to prevent water from flowing back into the sump pit after the pump shuts off. Install the check valve in the discharge pipe, close to the pump outlet. Make sure the valve is oriented correctly to allow water to flow only outwards.
-
Connecting the Float Switch. The float switch activates the pump when the water level rises. Ensure the float switch moves freely and is not obstructed. Adjust the tether or clip to set the desired activation level. Proper float switch function is critical for automatic operation.
-
Final Checks. Once everything is connected, double-check all fittings and connections to ensure they are tight and secure. Make sure the discharge pipe is properly supported and will direct water away from your foundation.
-
Testing the Pump. Plug the sump pump into the outlet. Slowly fill the sump pit with water using a hose. Observe the pump as the water level rises. The pump should automatically turn on when the float switch reaches its activation point. Ensure water is being discharged correctly, and the check valve is working properly.
Securing the Pump in the Sump Pit
Proper placement and stabilization of the sump pump within the pit are crucial for efficient operation and longevity.
-
Submersible Pumps: Place the pump on a solid, level surface within the pit. Use bricks or pavers to elevate it slightly off the bottom. This prevents the pump from drawing in sediment and debris that can clog the impeller.
-
Pedestal Pumps: Ensure the pedestal base is stable and secure. The motor housing must be positioned above the anticipated maximum water level in the pit.
Discharge Pipe and Check Valve Connection
The discharge pipe is how the water exits your home.
-
Proper Piping is Important. Use a rigid PVC pipe for the discharge line whenever possible. It’s more durable and less likely to kink or collapse than flexible hose.
-
Routing the Pipe: Ensure the discharge pipe slopes downward away from your home to promote efficient drainage. Avoid sharp bends or restrictions that can reduce flow.
-
Check Valve Orientation: The check valve must be installed with the arrow pointing in the direction of water flow (away from the pump). This prevents backflow and ensures the pump only works to remove water, not recirculate it.
Essential Safety Precautions
Safety is paramount when installing any electrical equipment, especially in damp environments.
-
Always disconnect power. Before starting work, turn off the circuit breaker that controls the outlet you’ll be using. Double-check with a circuit tester.
-
Wear appropriate safety gear. Use rubber gloves and eye protection to protect yourself from potential hazards.
-
Extension Cords. Avoid using extension cords if possible. If necessary, use a heavy-duty, grounded extension cord that is rated for outdoor use.
-
Ground Fault Circuit Interrupter (GFCI). Plug the sump pump into a GFCI outlet. GFCI outlets are designed to trip and cut off power in the event of an electrical fault, reducing the risk of electric shock. If you don’t have a GFCI outlet, consider having one installed by a qualified electrician.
By following these detailed instructions and prioritizing safety, you can ensure your oil sump pump is properly installed, providing reliable flood protection for your basement and home.
Maintenance Matters: Keeping Your Oil Sump Pump Running Smoothly
An oil sump pump is your home’s first line of defense against basement flooding, but its effectiveness hinges on regular maintenance. Neglecting this crucial aspect can lead to premature failure, leaving you vulnerable to costly water damage. Think of maintenance as an investment, safeguarding your property and providing peace of mind.
Why Regular Maintenance is Essential
Regular maintenance extends the life of your sump pump, ensures its reliable operation, and prevents costly repairs. A well-maintained pump operates at peak efficiency, saving energy and minimizing the risk of unexpected breakdowns, especially during critical times like heavy storms.
Creating a Maintenance Schedule
Establish a regular maintenance schedule. A quarterly inspection is a good starting point, increasing to monthly during periods of heavy rain or snowmelt. Mark these dates on your calendar as a reminder to keep your pump in top condition.
Cleaning the Sump Pit: Removing Debris and Preventing Clogging
The sump pit, where your pump sits, can accumulate sediment, debris, and even small objects over time. This build-up can clog the pump’s intake, hindering its ability to remove water effectively.
Here’s how to clean your sump pit:
-
Disconnect the Power: Always begin by disconnecting the power to the sump pump to avoid electrical hazards.
-
Remove the Pump: Carefully remove the sump pump from the pit.
-
Empty the Pit: Use a wet/dry vacuum or a bucket to remove any standing water and debris from the pit.
-
Clean the Pit Walls: Scrub the walls of the pit with a brush to remove any accumulated sediment or algae.
-
Rinse the Pit: Rinse the pit with clean water and remove any remaining debris.
-
Reinstall the Pump: Carefully reinstall the sump pump, ensuring it is sitting securely and not resting directly on the bottom of the pit.
Inspecting the Float Switch: Ensuring Proper Activation
The float switch is responsible for activating the pump when the water level rises. If the switch is stuck or malfunctioning, the pump may not turn on when needed, leading to flooding.
Here’s how to inspect the float switch:
-
Visual Inspection: Check the float switch for any signs of damage, such as cracks or breaks.
-
Freedom of Movement: Ensure the float switch moves freely up and down without any obstructions.
-
Test the Activation: Manually lift the float switch to simulate rising water levels and confirm that the pump activates. If the pump does not turn on, the float switch may need to be replaced.
Checking the Check Valve: Preventing Backflow
The check valve prevents water from flowing back into the sump pit after the pump has discharged it. A malfunctioning check valve can reduce the pump’s efficiency and potentially lead to flooding.
Here’s how to check the check valve:
-
Visual Inspection: Inspect the check valve for any signs of damage or leaks.
-
Listen for Backflow: After the pump has finished discharging water, listen for any gurgling sounds that may indicate water flowing back into the pit.
-
Manual Test: If possible, manually check the check valve to ensure it is closing properly and preventing backflow. If the check valve is not functioning correctly, it may need to be replaced.
Additional Maintenance Tips
-
Periodically pour a bucket of water into the sump pit to ensure the pump activates and discharges water effectively.
-
Inspect the discharge pipe for any clogs or obstructions.
-
Consider a professional inspection by a qualified plumber to ensure your sump pump system is in optimal condition.
By following these maintenance tips, you can significantly extend the life of your oil sump pump, ensuring it’s ready to protect your home from flooding whenever the need arises. Don’t wait until disaster strikes; a little preventative maintenance can save you a lot of heartache and expense in the long run.
Maintenance is essential for a long-lasting sump pump, but even the most diligent homeowner can’t control everything. Power outages, especially during severe storms, can render your primary sump pump useless, leaving your basement vulnerable. That’s where a reliable backup power solution becomes absolutely critical.
Backup Power Solutions: Protecting Your Basement During Power Outages
A flooded basement is a nightmare scenario. It’s even more frustrating when it happens because of something beyond your control, like a power outage during a torrential downpour. While a well-maintained primary sump pump is your first line of defense, a backup power system is your safety net, ensuring continued protection when the electricity goes out.
Why a Backup Sump Pump is Essential
Imagine a scenario: a major storm hits, knocking out power lines across your neighborhood. The rain is relentless, and water is quickly accumulating around your home’s foundation. Your primary sump pump, normally a steadfast guardian, is now silent, rendered useless without electricity.
Without a backup, the rising water can quickly overwhelm your basement, leading to:
- Costly water damage to walls, flooring, and possessions.
- Mold growth, creating health hazards and requiring expensive remediation.
- Electrical hazards from submerged outlets and wiring.
- The heartbreaking loss of sentimental or irreplaceable items.
A backup sump pump system offers peace of mind, knowing that even during a power outage, your basement remains protected.
Exploring Battery Backup Options
The most common and practical solution for backup power is a battery backup system. These systems typically consist of:
- A dedicated battery (usually marine-grade deep cycle).
- A charger/inverter unit.
- A secondary sump pump (often DC-powered).
When the power goes out, the system automatically switches to battery power, activating the backup pump to continue removing water from the sump pit.
Understanding Runtime and Charging
The runtime of a battery backup system depends on several factors:
- Battery capacity (measured in amp-hours).
- The pump’s energy consumption (wattage or amperage).
- The frequency and duration of pump activation (how often the pump needs to run).
Deep-cycle batteries are designed to be discharged and recharged repeatedly, making them ideal for sump pump backup systems.
The charger/inverter unit constantly monitors the battery’s charge level and automatically recharges it when power is restored.
Considerations for Choosing a Battery
When selecting a battery, prioritize amp-hours (Ah). A higher Ah rating translates to a longer runtime. Consider also:
- Battery type: Opt for a deep-cycle marine battery designed for repeated discharging and recharging.
- Maintenance: Some batteries require periodic maintenance (adding water), while others are maintenance-free.
- Warranty: A longer warranty can provide added peace of mind.
Sizing Your Backup System for Extended Power Losses
Choosing the right size backup system is crucial for ensuring adequate protection during extended outages. Don’t make the mistake of thinking all systems are the same.
Here’s how to approach sizing:
-
Assess your area’s rainfall: Research the average rainfall intensity and duration during storms in your region. Your local weather authority can provide this data.
-
Determine your sump pump’s pumping capacity: Know how many gallons per hour (GPH) your primary pump removes. The backup pump should ideally match or exceed this capacity.
-
Calculate estimated runtime: Estimate how long your pump will need to run on battery power during a typical outage. Account for the frequency and duration of pump cycles.
-
Choose the appropriate battery: Select a battery with sufficient amp-hours to power your backup pump for the estimated runtime. It’s always better to overestimate than underestimate.
Consult with a sump pump professional for personalized recommendations and assistance in sizing your backup system. They can provide expert advice based on your specific needs and circumstances.
Maintenance is essential for a long-lasting sump pump, but even the most diligent homeowner can’t control everything. Power outages, especially during severe storms, can render your primary sump pump useless, leaving your basement vulnerable. That’s where a reliable backup power solution becomes absolutely critical.
Even with a top-of-the-line sump pump and a robust backup system, problems can still arise. Being able to diagnose and address these issues yourself can save you time, money, and the stress of dealing with a flooded basement. Let’s dive into some common sump pump problems and how to tackle them.
Troubleshooting: Diagnosing and Fixing Common Sump Pump Problems
A malfunctioning sump pump can quickly turn into a homeowner’s nightmare. Recognizing the signs of trouble and knowing how to troubleshoot common issues can save you from costly water damage and the headache of calling a professional.
The Case of the Stuck or Malfunctioning Float Switch
The float switch is the unsung hero of your sump pump system. It’s responsible for detecting rising water levels and activating the pump. If it’s stuck or malfunctioning, your pump may not turn on when it should, or worse, it might run continuously.
Identifying a Float Switch Issue
Is the pump not turning on even when water is in the pit?
Is the pump running constantly, even when the water level is low?
These are telltale signs of a float switch problem.
Troubleshooting the Float Switch
Check for Obstructions: The first step is to visually inspect the float switch. Debris, such as gravel, dirt, or even the pump’s power cord, can obstruct the float’s movement. Carefully remove any obstructions.
Test the Float: Gently lift the float switch. It should move freely and activate the pump. If it feels stiff or doesn’t trigger the pump, it may be damaged.
Clean the Float: Over time, the float switch can accumulate grime and buildup. Clean it with a damp cloth to ensure smooth operation.
Replace if Necessary: If cleaning and removing obstructions doesn’t resolve the issue, the float switch itself may be faulty and need replacement. These are relatively inexpensive and easy to replace. Disconnect the power, detach the old switch, and install the new one following the manufacturer’s instructions.
Tackling a Clogged or Frozen Discharge Pipe
The discharge pipe is responsible for carrying water away from your home. If it becomes clogged or frozen, water can back up into the sump pit, potentially leading to flooding.
Diagnosing a Clogged Discharge Pipe
Is water pooling around the sump pit, even when the pump is running?
Is the pump running but not discharging water?
Is there significantly reduced water flow from the discharge pipe outlet?
These are signs that your discharge pipe might be blocked.
Clearing a Clogged Discharge Pipe
Check the Outlet: Start by inspecting the outlet of the discharge pipe. Leaves, debris, or ice can accumulate and block the flow of water. Clear any visible obstructions.
Flush the Pipe: Use a garden hose with a high-pressure nozzle to flush out the discharge pipe. Insert the hose into the outlet and force water back through the pipe to dislodge any clogs.
Consider a Plumbing Snake: For stubborn clogs, a plumbing snake can be used to break up and remove the obstruction. Carefully insert the snake into the discharge pipe and work it through the blockage.
Preventing a Frozen Discharge Pipe
Insulate the Pipe: Wrap the exposed sections of the discharge pipe with pipe insulation to prevent freezing during cold weather.
Install a Freeze Relief Valve: A freeze relief valve allows water to escape if the pipe freezes, preventing pressure buildup that can damage the pump.
Angle the Pipe: Ensure the discharge pipe has a slight downward slope to allow water to drain away from the house, reducing the risk of freezing.
When the Pump Won’t Turn On
Perhaps the most alarming scenario is when your sump pump simply refuses to turn on, even when the float switch is activated and water is accumulating in the pit.
Investigating a Non-Responsive Pump
Is the pump completely silent when the float switch is lifted?
Have you checked the power source and confirmed it is working?
These indicate a more serious problem that requires immediate attention.
Troubleshooting a Pump That Won’t Start
Check the Power Supply: This is the most basic but often overlooked step. Make sure the pump is plugged in securely and that the circuit breaker hasn’t tripped. Reset the breaker if necessary.
Inspect the Power Cord: Examine the power cord for any signs of damage, such as cuts or frays. A damaged cord can prevent the pump from receiving power. Replace the cord if necessary, or consult an electrician.
Test the Pump Motor: If the power supply is fine, the pump motor itself may be faulty. You can test the motor with a multimeter to check for continuity. If the motor is dead, the pump will need to be replaced.
Overheating Protection: Many sump pumps have a thermal overload protector that will shut the pump off if it overheats. Allow the pump to cool down for 20-30 minutes, and it may reset itself.
By systematically addressing these common issues, you can keep your sump pump running smoothly and protect your basement from the devastating effects of flooding. Remember, safety is paramount. Always disconnect the power supply before attempting any repairs. When in doubt, consult a qualified plumber or electrician.
FAQs: Oil Sump Pump Lifesaver
Here are some common questions about oil sump pumps and how they can help prevent flooding.
How often should I check my oil sump pump?
It’s best to check your oil sump pump at least every 3-4 months to ensure it’s functioning correctly. More frequent checks during periods of heavy rain or snowmelt are recommended. Look for any signs of debris clogging the intake or unusual noises during operation.
What are the benefits of using an oil sump pump over an electric one?
Oil sump pumps are often more reliable during power outages, as they can be powered by a backup generator or manually. They also tend to last longer and require less frequent maintenance compared to electric models, offering a potentially more cost-effective solution long-term.
Can I install an oil sump pump myself?
While some homeowners opt for DIY installation, it’s generally recommended to have a professional plumber install an oil sump pump. Proper installation is crucial to ensure it functions correctly and to avoid potential hazards associated with oil and electrical components. A professional can also advise on the best placement and size for your specific needs.
How do I maintain my oil sump pump to prolong its lifespan?
Regular maintenance includes checking the oil level and changing it according to the manufacturer’s recommendations. Also, inspect the pump for any signs of leaks, corrosion, or debris buildup. Keeping the sump pit clean will help prevent the oil sump pump from clogging and ensure optimal performance.
Alright, you’ve got the lowdown on keeping your basement dry with an oil sump pump! Hopefully, you’re feeling confident and ready to tackle any potential flooding issues. Stay dry out there!