Adhesive selection represents a critical decision when undertaking woodworking projects. Loctite, a product of Henkel, primarily targets metal bonding; however, its efficacy when used on wood substrates requires careful consideration. The type of wood, alongside factors such as joint strength, influence the overall performance. Therefore, the central question remains: does loctite work on wood? Exploring joint strength and application specifics provides clarity concerning whether Loctite is indeed suitable for wooden assemblies.
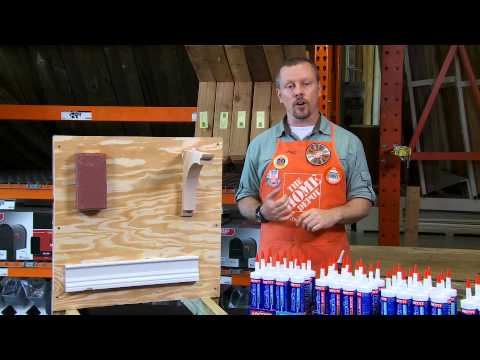
Image taken from the YouTube channel The Home Depot Pro Channel , from the video titled OSI Loctite Power Grab for Pros – The Home Depot .
Loctite, a name synonymous with industrial-strength bonding, has become a staple in various fields, from automotive repair to electronics manufacturing. Its reputation for creating durable, reliable seals and bonds on materials like metal and plastics is well-deserved. But what happens when this powerhouse adhesive is pitted against a material as unique and complex as wood?
The question isn’t simply can Loctite adhere to wood, but how well does it perform, and is it the right choice for woodworking projects?
The Central Question: Does Loctite Work on Wood?
This is the query we aim to dissect. While Loctite boasts impressive adhesion capabilities on many surfaces, wood presents particular challenges due to its porous nature and inherent flexibility. Can Loctite overcome these hurdles, or does its rigid composition make it a less-than-ideal candidate for woodworking applications?
Article Purpose and Scope
This article serves as an objective analysis of Loctite’s effectiveness on wood. We will explore its capabilities, limitations, and suitability for various woodworking tasks. Furthermore, we’ll conduct a comparative analysis against traditional wood glues. This time-honored adhesive is formulated explicitly for wood’s unique properties.
By examining Loctite’s performance alongside that of wood glue, we hope to provide you with the insights needed to make informed decisions. Choosing the correct adhesive is paramount for the success and longevity of your woodworking projects.
Loctite’s performance on wood may be questionable, but to fully understand why, it’s essential to delve into the characteristics that make Loctite what it is. Its unique chemical makeup and application parameters will help determine how suitable it is for adhering wood.
Understanding Loctite: Composition, Properties, and Ideal Uses
Loctite is more than just a brand name; it represents a wide range of adhesives, sealants, and threadlockers designed for industrial and consumer applications. To assess its potential in woodworking, we must first understand its composition, properties, and intended applications.
What Exactly is Loctite?
At its core, Loctite refers to a family of acrylic-based adhesives.
Many formulations are based on cyanoacrylate, epoxy, or anaerobic chemistry.
Different types cater to specific bonding needs.
Threadlockers, for example, are designed to prevent loosening of fasteners due to vibration.
Instant adhesives (super glues) offer rapid bonding.
Structural adhesives provide high-strength, load-bearing capabilities.
Each type exhibits distinct chemical compositions and properties.
This variation is crucial when considering suitability for a particular application like woodworking.
Loctite’s Typical Applications
Loctite products are widely used in industries where strong, durable, and reliable bonds are critical.
These applications range from automotive assembly and electronics manufacturing to aerospace engineering.
In these scenarios, Loctite offers several key advantages:
-
High Strength: Loctite formulations can create incredibly strong bonds, often exceeding the strength of the materials being joined.
-
Chemical Resistance: Many Loctite products are resistant to oils, solvents, and other chemicals, ensuring long-term performance in harsh environments.
-
Temperature Resistance: Certain formulations can withstand extreme temperatures, making them suitable for demanding applications.
-
Precision Bonding: Loctite allows for precise application, minimizing waste and ensuring accurate alignment.
The material composition used in these applications are often metals and plastics.
These are materials that don’t have the same porous or flexible properties of wood.
Key Properties and Limitations
Several key properties define Loctite’s performance:
-
Bonding Strength: Loctite is known for its ability to form strong bonds between various materials. The strength of the bond can vary significantly depending on the specific formulation and the materials being joined.
-
Cure Speed: Cure time is a significant factor, as some Loctite products offer rapid curing, significantly speeding up assembly processes.
-
Viscosity: Viscosity refers to the thickness of the adhesive, affecting its ability to penetrate small gaps and porous materials.
-
Gap Filling: Some Loctite adhesives have excellent gap-filling capabilities, which is crucial when bonding uneven surfaces.
-
Chemical Resistance: Resistance to solvents, oils, and other chemicals is essential for applications in harsh environments.
However, Loctite also has limitations:
-
Surface Preparation: Many Loctite products require clean, dry surfaces for optimal bonding. Contaminants like oil, grease, or dust can significantly weaken the bond.
-
Material Compatibility: Not all Loctite formulations are compatible with every material. Some may not bond well to certain plastics or may damage sensitive surfaces.
-
Brittleness: Some Loctite adhesives can be brittle, making them susceptible to cracking or failure under impact or vibration.
-
Cost: Compared to traditional adhesives like wood glue, Loctite can be more expensive, especially for large-scale applications.
Loctite’s performance on wood may be questionable, but to fully understand why, it’s essential to delve into the characteristics that make Loctite what it is. Its unique chemical makeup and application parameters will help determine how suitable it is for adhering wood.
Wood: A Unique Material for Bonding
Wood presents a distinct set of challenges compared to many other materials commonly bonded with adhesives. Its inherent structure and properties demand a specialized approach to achieve strong and lasting connections. Understanding these nuances is crucial for successful woodworking and for evaluating the appropriateness of adhesives like Loctite.
The Porous and Fibrous Nature of Wood
Unlike the smooth, uniform surfaces of metal or plastic, wood is inherently porous and fibrous. This complex structure stems from its composition of cellulose fibers, lignin, and various extractives.
These components create a network of interconnected cells and vessels.
This network allows wood to absorb moisture and expand or contract with changes in humidity.
These characteristics significantly impact adhesive bonding.
Challenges in Bonding Wood
The porous nature of wood, while offering some advantages in terms of mechanical keying, also presents challenges:
-
Absorption: Wood’s ability to absorb liquids can lead to adhesives being drawn deep into the wood, resulting in a glue-starved joint. The surface may appear to have sufficient adhesive, but the actual bond line lacks adequate material.
-
Moisture Content: Changes in wood’s moisture content can stress adhesive bonds. As wood expands and contracts, it can weaken the bond or even cause it to fail over time.
-
Surface Irregularities: Wood surfaces are rarely perfectly smooth. Variations in grain, knots, and other imperfections can create uneven bonding surfaces, leading to inconsistent adhesion.
Surface Preparation: A Critical Step
Given these challenges, proper surface preparation is paramount for successful wood bonding.
It’s the foundation upon which a strong and durable joint is built.
Surface preparation methods can include:
-
Cleaning: Removing dirt, dust, oil, and other contaminants that can interfere with adhesion.
-
Sanding: Creating a smooth, even surface and opening up the wood’s pores to enhance mechanical keying.
-
Jointing/Planing: Ensuring that mating surfaces are flat and precisely aligned for optimal contact.
-
Degreasing: Removing natural oils from certain wood species that can inhibit bonding.
By addressing these factors through careful surface preparation, woodworkers can significantly improve the likelihood of achieving a strong and long-lasting bond, regardless of the adhesive used.
Wood’s inherent complexities pose unique challenges to adhesion. Now, how does Loctite fare when put to the test against this organic material? Let’s delve into a controlled experiment designed to evaluate its performance on various wood types.
The Experiment: Loctite’s Performance on Various Wood Types
To ascertain Loctite’s effectiveness on wood, a carefully designed experiment was conducted. This involved testing various Loctite products on different wood species under controlled conditions. The goal was to objectively evaluate the initial bonding quality, strength, and any potential adverse effects.
Experimental Setup: A Detailed Overview
The experiment’s setup was meticulously planned to minimize confounding variables and ensure reliable results.
Wood Sample Selection
Three common wood types were selected for the experiment:
-
Pine: Chosen for its soft, porous nature and affordability, representing a commonly used softwood.
-
Oak: Selected for its hardness, density, and prominent grain pattern, representing a durable hardwood.
-
Maple: Chosen for its fine grain, closed pores, and moderate hardness, representing a versatile hardwood often used in furniture making.
Each wood type was prepared into uniform samples of specific dimensions to ensure consistent bonding surface area.
Loctite Product Selection
A range of Loctite products were chosen to represent different adhesive chemistries and application methods:
-
Loctite Super Glue: A cyanoacrylate adhesive known for its rapid bonding time and high strength on non-porous surfaces.
-
Loctite Threadlocker (Blue 242): Primarily designed for locking threaded fasteners, but included to assess its adhesive properties on wood.
-
Loctite Construction Adhesive: A general-purpose adhesive formulated for construction materials, including wood.
Application and Curing
Each Loctite product was applied to the wood samples according to the manufacturer’s instructions. Clamps were used to ensure consistent pressure during the curing process.
Curing times were strictly adhered to based on the product specifications. Environmental conditions (temperature and humidity) were monitored and controlled throughout the experiment.
Initial Observations: Bonding Quality and Strength
Following the curing period, the bonded wood samples were carefully examined and tested for initial bonding quality and strength.
Bonding Quality Assessment
The initial bonding quality was assessed visually, noting the following:
-
Adhesive Spread: How well the adhesive spread across the bonding surface.
-
Surface Wetting: The adhesive’s ability to wet and penetrate the wood surface.
-
Bond Line Appearance: The uniformity and consistency of the adhesive bond line.
Strength Testing
The initial strength of the Loctite bonds was evaluated using a combination of methods:
-
Tensile Testing: Measures the force required to pull the bonded wood samples apart in a direct tension.
-
Shear Testing: Measures the force required to slide the bonded wood samples apart in a parallel direction.
-
Qualitative Assessment: Manually attempting to separate the bonded samples to gauge the bond’s resistance to force.
Visible Issues: Bleeding and Discoloration
Throughout the experiment, any visible issues, such as bleeding or discoloration, were carefully documented.
-
Bleeding: Adhesive seeping into the surrounding wood, potentially affecting the finish.
-
Discoloration: Changes in the wood’s color due to the adhesive’s chemical interaction.
The presence and extent of these issues were noted for each Loctite product and wood type combination. These observations offered valuable insights into the compatibility of Loctite with wood.
Wood’s inherent complexities pose unique challenges to adhesion. Now, how does Loctite fare when put to the test against this organic material? Let’s delve into a controlled experiment designed to evaluate its performance on various wood types.
Loctite vs. Wood Glue: A Head-to-Head Comparison
The world of woodworking and material bonding often presents a crucial decision: which adhesive reigns supreme? While Loctite boasts a strong reputation for its efficacy on metal and plastics, wood presents a different arena. To truly understand where Loctite stands, we must pit it against the time-tested champion of woodworking: wood glue.
This section provides an in-depth comparative analysis, dissecting the strengths and weaknesses of each adhesive to illuminate their ideal applications.
Wood Glue: The Traditional Choice
Wood glue, specifically formulated for wood’s unique properties, has long been the go-to adhesive for carpenters and woodworkers. Its formulation is tailored to penetrate wood fibers, creating a robust and lasting bond.
Advantages of Wood Glue
Specifically Designed for Wood: Wood glue’s chemical composition is optimized to interact with wood’s cellular structure, ensuring maximum adhesion and penetration. This specialized formulation allows for a strong, reliable bond that takes into account wood’s natural expansion and contraction.
Durability: Wood glue creates bonds that are generally more durable and resistant to stress, especially in woodworking applications where structural integrity is paramount.
Sandability and Paintability: Wood glues are formulated to be easily sanded and painted once cured, providing a seamless finish that integrates with the surrounding wood. This is crucial for achieving professional-looking results in woodworking projects.
Disadvantages of Wood Glue
Longer Curing Time: Compared to Loctite’s rapid bonding, wood glue typically requires a longer curing time, often necessitating clamping for several hours. This extended wait can slow down project completion.
Not Ideal for All Materials: Wood glue is specifically designed for wood and may not perform well on other materials like metal or plastic.
Loctite: The Fast-Acting Alternative
Loctite, known for its industrial and general-purpose adhesives, offers a different approach to bonding. Its appeal lies in its quick-setting nature and impressive strength on certain materials. However, its performance on wood requires careful consideration.
Advantages of Loctite
Faster Curing Time: Loctite’s most significant advantage is its rapid curing time. This quick bonding action can be invaluable in situations where speed is essential, offering immediate results.
High Initial Strength: Some Loctite formulations, particularly super glues, exhibit high initial strength, allowing for immediate handling of bonded components.
Disadvantages of Loctite
Potential for Brittle Bonds: Loctite bonds can sometimes be brittle, especially under stress or impact. This brittleness can compromise the joint’s long-term durability, particularly in woodworking applications that require flexibility.
Poor Penetration: Wood’s porous nature requires adhesives that can penetrate the surface fibers for a strong bond. Loctite, especially thinner formulations, may not effectively penetrate wood, resulting in a weaker, surface-level connection.
Not Specifically Formulated for Wood: Loctite’s general-purpose formulation isn’t optimized for wood’s unique properties, potentially leading to less reliable bonds compared to wood glue.
Scenarios: When to Choose Which
The choice between Loctite and wood glue hinges on the specific demands of the woodworking project.
Wood glue is superior in scenarios requiring:
- High structural integrity and long-term durability.
- Projects involving large surface areas or complex joints.
- Situations where sanding and finishing are essential.
Loctite could be considered in scenarios where:
- A quick, temporary fix is needed.
- Reinforcing small joints that are already mechanically sound.
- Bonding wood to non-porous materials where wood glue might not adhere well.
However, it’s crucial to acknowledge that Loctite on wood often involves compromise, particularly regarding long-term durability.
Ultimately, the best adhesive is the one that aligns with the project’s specific requirements and material properties. While Loctite may offer a quick fix, wood glue remains the gold standard for achieving strong, lasting bonds in most woodworking applications.
Wood glue’s superior performance in many initial tests begs the question: how do these adhesives hold up over time? The true test of any adhesive lies not just in its initial grab, but in its ability to withstand the relentless forces of nature and the passage of time. This section delves into the crucial aspect of long-term durability, specifically focusing on the impact of environmental factors on Loctite bonds when applied to wood, and how they stack up against the enduring reliability of wood glue.
Long-Term Durability: Assessing Environmental Impact
The longevity of an adhesive bond is a critical factor, particularly in woodworking projects intended to withstand years of use and exposure. Environmental elements like humidity and temperature fluctuations can significantly impact the integrity of adhesive bonds, leading to weakening, cracking, or even complete failure. To truly assess the viability of Loctite for woodworking, a rigorous examination of its long-term durability is essential.
The Testing Protocol: Simulating Real-World Conditions
To effectively gauge long-term performance, accelerated aging tests are employed. These tests expose bonded wood samples to controlled cycles of high humidity, extreme temperatures (both hot and cold), and UV radiation to simulate years of environmental stress in a condensed timeframe.
Specifically, the samples are subjected to:
-
Humidity Cycling: Alternating periods of high and low humidity to simulate seasonal changes and moisture exposure.
-
Thermal Cycling: Exposure to temperature extremes, mimicking the expansion and contraction of wood due to temperature fluctuations.
-
UV Exposure: Simulated sunlight exposure to assess the adhesive’s resistance to degradation from ultraviolet rays.
These tests aim to replicate the harsh conditions that woodworking projects often face, providing a reliable indication of how the adhesive bonds will perform over extended periods.
Environmental Factors and Their Impact on Bonding Integrity
Wood is a hygroscopic material, meaning it readily absorbs and releases moisture from the surrounding air. This inherent property of wood poses a significant challenge to adhesive bonds.
Humidity
High humidity levels can cause wood to swell, while low humidity leads to shrinkage. These dimensional changes create stress on the adhesive bond. Loctite, particularly cyanoacrylate-based super glues, tend to form rigid, inflexible bonds. This inflexibility makes them more susceptible to cracking or failure when subjected to the cyclical expansion and contraction of wood caused by humidity changes.
Wood glue, on the other hand, is formulated to be more flexible and can better accommodate the wood’s natural movement.
Temperature
Extreme temperature fluctuations can also weaken adhesive bonds. As wood heats up, it expands, and as it cools down, it contracts. This constant expansion and contraction can fatigue the adhesive, especially if it is not able to move with the wood.
The different coefficients of thermal expansion between Loctite and wood can cause shearing stresses at the bond line. This stress can lead to delamination or bond failure, particularly with rigid Loctite formulations.
UV Radiation
Exposure to ultraviolet (UV) radiation from sunlight can degrade certain adhesives, causing them to become brittle and lose their adhesive properties. While some Loctite formulations offer UV resistance, many are susceptible to UV degradation over time. This can be a significant concern for outdoor woodworking projects.
Comparative Analysis: Loctite vs. Wood Glue
The long-term durability testing reveals a clear distinction between Loctite and wood glue’s performance under environmental stress:
-
Wood Glue: Generally exhibits superior long-term durability in woodworking applications. Its flexible nature allows it to better accommodate the wood’s natural movement, resisting cracking and bond failure under fluctuating humidity and temperature conditions. Many wood glues are also formulated with UV-resistant additives, making them suitable for outdoor projects.
-
Loctite: While certain Loctite formulations may perform adequately in controlled indoor environments, they often struggle to withstand the rigors of outdoor exposure and fluctuating environmental conditions. The rigidity of many Loctite adhesives makes them prone to cracking and failure when subjected to the dimensional changes of wood caused by humidity and temperature variations. Furthermore, susceptibility to UV degradation can limit their lifespan in outdoor applications.
In essence, while Loctite might offer a quick fix or temporary solution in specific scenarios, wood glue remains the champion for projects demanding long-term durability and resilience in the face of environmental challenges. Its formulation is inherently better suited to the dynamic nature of wood, ensuring a lasting and reliable bond.
Wood glue demonstrates its reliability and resilience over extended periods, holding firm against the elements. However, this isn’t to say that Loctite has no place in the workshop. Certain niche applications exist where its unique properties might offer a pragmatic solution, especially when time is of the essence or the required bond is not structural in nature.
Niche Applications: When Could Loctite Be Useful in Woodworking?
While wood glue remains the adhesive of choice for most woodworking projects demanding long-term durability and structural integrity, Loctite products can find utility in specific, less demanding scenarios. The key is to understand the limitations of Loctite on wood and to carefully evaluate the project’s specific needs before reaching for that familiar red bottle.
Temporary Fixes and Clamping Alternatives
Loctite’s rapid curing time can be a significant advantage in situations where a quick, temporary hold is required. Imagine a scenario where you need to temporarily attach a jig to a workpiece, or perhaps hold a small piece in place while wood glue cures on a primary joint. In such cases, a small amount of Loctite can act as a fast-acting clamp, freeing up your hands and speeding up the workflow.
However, it’s crucial to remember that this is a temporary solution. The Loctite bond should not be relied upon for long-term structural support and should be easily removable once the primary adhesive has cured.
Reinforcing Small, Non-Structural Joints
In certain delicate woodworking tasks, such as crafting intricate inlays or assembling small decorative pieces, the strength requirements are minimal. Loctite, particularly cyanoacrylate (super glue) formulations designed for porous materials, could provide sufficient bonding for these light-duty applications.
For example, adhering thin veneers or reinforcing the edges of small, non-load-bearing joints might be suitable use cases.
It’s essential to ensure that the Loctite used is compatible with wood, that the surfaces are properly prepared, and that the joint is not subjected to significant stress.
Repairing Minor Defects
Loctite can be a handy tool for addressing minor imperfections in wood. Small cracks, chips, or splinters can be quickly repaired with a dab of super glue, providing a seamless and often invisible fix. This can be particularly useful for restoring antique furniture or repairing delicate wooden objects.
However, it’s crucial to use Loctite sparingly and to avoid over-application, as excess adhesive can be difficult to remove and may create an unsightly appearance. Also, consider that epoxy wood fillers might be better suited for larger defects.
Stabilizing End Grain
End grain, with its open pores, is notoriously difficult to glue effectively. While wood glue can still be used, Loctite, particularly penetrating formulations, might offer some initial stabilization by soaking into the fibers.
This can be especially helpful when working with end grain joints that require subsequent shaping or sanding. However, this should be considered a supplement to wood glue, not a replacement.
Project-Specific Requirements are Paramount
Ultimately, the decision to use Loctite in woodworking should be driven by a thorough assessment of the project’s specific requirements. Consider the following factors:
- Load-bearing capacity: Will the joint be subjected to significant stress or weight?
- Environmental conditions: Will the project be exposed to moisture, temperature fluctuations, or UV radiation?
- Aesthetics: Will the Loctite affect the appearance of the finished product?
- Longevity: How long is the bond expected to last?
- Material Compatibility: Is the Loctite formulation safe and effective for the specific wood species used?
By carefully weighing these factors, you can determine whether Loctite is a suitable adhesive for your woodworking project, or whether wood glue remains the more reliable and appropriate choice. Err on the side of caution and choose the solution that provides the greatest degree of strength and long-term durability.
The Verdict: Does Loctite Actually Work on Wood?
After thorough examination and testing, the answer to whether Loctite "works" on wood is nuanced. While Loctite can create a bond with wood, its suitability for woodworking is generally limited. It’s crucial to understand these limitations to avoid project failures and ensure lasting results.
The Short Answer: Proceed with Caution
Loctite, particularly cyanoacrylate-based super glues, can indeed adhere to wood surfaces. The initial bond can be surprisingly strong, especially on smooth, well-prepared surfaces.
However, this initial strength often masks underlying weaknesses that become apparent over time and under stress. For projects demanding long-term structural integrity, Loctite typically falls short compared to traditional wood glues.
Understanding the Limitations of Loctite on Wood
Several factors contribute to Loctite’s less-than-ideal performance on wood.
-
Brittle Bond: Loctite tends to form a rigid, brittle bond. Wood, being a natural and somewhat flexible material, expands and contracts with changes in humidity and temperature.
This movement can cause the rigid Loctite bond to crack or fail over time, especially in larger assemblies.
-
Poor Penetration: Unlike wood glues that penetrate the wood fibers to create a strong mechanical bond, Loctite primarily adheres to the surface.
This lack of penetration results in a weaker bond, particularly on porous wood species.
-
Incompatibility with Wood Movement: Wood is hygroscopic, meaning it absorbs and releases moisture.
This process causes it to swell and shrink. Loctite, being a rigid adhesive, doesn’t accommodate this natural movement well.
The resulting stress can lead to bond failure.
-
Chemical Incompatibility: Some Loctite formulations can react negatively with certain wood finishes or preservatives, potentially weakening the bond or causing discoloration.
Choosing the Right Adhesive: A Matter of Project Requirements
The world of adhesives offers a plethora of options, each with its strengths and weaknesses. For woodworking, selecting the right adhesive is paramount to the project’s success and longevity.
Before reaching for any adhesive, consider the following factors:
-
Structural Requirements: Is the joint load-bearing?
If so, wood glue is almost always the superior choice. -
Wood Type: Some woods are more porous or oily than others.
This will affect adhesive penetration and bond strength. -
Environmental Conditions: Will the project be exposed to moisture, heat, or extreme temperature fluctuations?
-
Curing Time: How quickly do you need the bond to set?
While Loctite offers speed, wood glue provides superior long-term strength.
The Bottom Line: Knowing When to Use Loctite (and When Not To)
While Loctite is not a universal solution for woodworking, it can be useful for very specific applications where speed and a non-structural bond are acceptable. However, for the vast majority of woodworking projects, especially those requiring strength, durability, and long-term reliability, traditional wood glue remains the undisputed champion.
Careful consideration of the project’s requirements and the adhesive’s properties is crucial for achieving successful and lasting results. Don’t let the allure of a quick fix compromise the integrity of your woodworking endeavors.
Loctite on Wood: Frequently Asked Questions
This FAQ section addresses common questions about using Loctite adhesives on wood surfaces.
Is Loctite a good choice for bonding wood?
Generally, no. While does loctite work on wood in some specific instances, it’s not the ideal adhesive for most woodworking projects. Wood glue is typically stronger and designed specifically for porous wood surfaces.
Why isn’t Loctite recommended for most wood applications?
Loctite, particularly threadlockers, are formulated for metal-to-metal bonding. Wood is porous and requires an adhesive that can penetrate its fibers to create a strong bond. Does loctite work on wood? Only if the wood is pre-treated and the bond is not structural.
When might Loctite be suitable for wood?
In very specific cases, Loctite might be useful. For example, a small amount of Loctite Super Glue could temporarily fix a small, non-structural part. However, it is not a long-term reliable solution. Does loctite work on wood reliably? No, not in load-bearing situations.
What alternatives are better than Loctite for woodworking?
Consider using wood glue, epoxy, or polyurethane adhesives. These adhesives are designed to penetrate wood fibers, provide strong bonds, and withstand the stresses typical in woodworking projects.
So, does loctite work on wood? Hopefully, now you have a better idea of whether it’s the right choice for your project. Happy building!